New recycling techniques aim to give colorants a second life
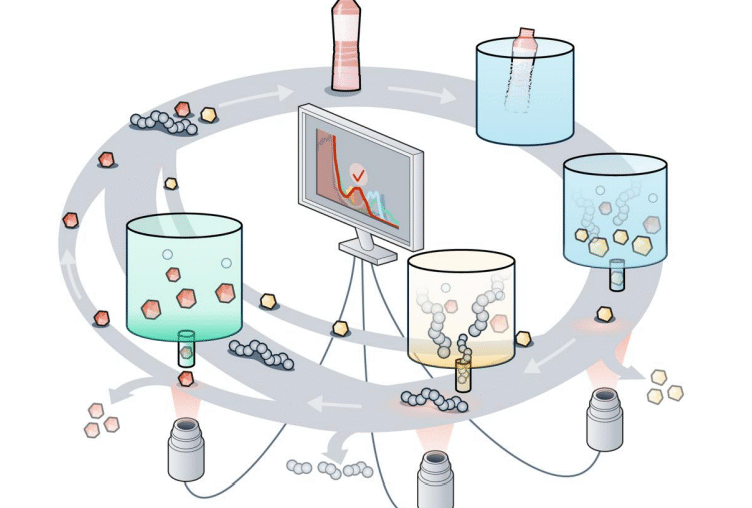
Over the next five years, Bert Weckhuysen will investigate how colorants from plastic bottles can be recycled more effectively. In August, he received a grant from the initiative Circular Plastics NL, funded by the Dutch National Growth Fund. Weckhuysen is collaborating with Jules Roelofs from Holland Colours, a manufacturer of colour concentrates, and CuRe Technology, a plastic recycling company.
Walk through any supermarket and you will see shelves lined with plastic bottles in every colour of the rainbow: green, red, blue – added to plastics to make packaging more appealing. But what happens to all those colorants once the bottle is empty and sent for recycling? At present, not much. Most colorants are lost in the recycling process as the plastic is often burned or, at best, reused. According to Bert Weckhuysen, Distinguished University Professor of Catalysis, Energy, and Sustainability at Utrecht University, this needs to change.
Thanks to a grant from Circular Plastics NL, Weckhuysen now has five years to explore how colorants in plastics can be recycled. Together with Holland Colours and CuRe Technology, his research group aims to develop technologies to recover both inorganic pigments and organic dyes from polyesters, evaluate their quality, and reuse them in recycled materials.
The value of colorants
Colorants in plastics are often lost during the recycling process – a missed opportunity, says Weckhuysen. “Colorants and other additives give PET bottles their desirable properties and therefore their value,” he explains. “These molecules are often expensive to produce and have a significant environmental footprint. What if we could recover those colorants and reuse them, just like we aim to do with the plastic itself?”
Greener solvents
Recycling colorants requires an overhaul of the current recycling process. “Right now, the focus is primarily on recycling the polymers – the long chains of atoms that form plastics,” says Weckhuysen. To include the colorants in this process, they first need to be extracted from the plastic.
This is where solvents come in, but many commonly used solvents are harmful to the environment. Weckhuysen’s team is taking a different approach: “We are opting for greener solvents made from bio-waste, making the entire process more sustainable.” This approach, which Weckhuysen calls ‘double green’, ensures that both the colorants and the plastic are given a second life in a more environmentally friendly way.
Washed-out T-shirt
Weckhuysen compares the way colorants are embedded in plastic to the color in clothing. “Think of a red T-shirt that has been washed dozens of times,” he says. “The color isn’t part of the fibers themselves but attached to them. Over time, colorant particles loosen, and the T-shirt fades – great for a bike ride, but not for a party,” he laughs. Similarly, colorant particles in plastic are interwoven with the long molecular chains and can be detached under certain conditions. “This gives us the opportunity to extract the colorants and reuse them”, he adds.
Step by step
The team has already devised a roadmap for extracting colorants from PET bottles. First, the colored PET bottles are dissolved in bio-based solvents, separating the colorants from the polymers. Next, they use light-based spectroscopy to determine which colorants are still usable. This technique allows the team to distinguish between damaged and intact colorant molecules, identifying which ones can go through another cycle. The usable molecules are then filtered out for reuse. “It’s a process of refinement,” Weckhuysen explains. “Every usable colorant we recover is another step closer to a fully circular system.”
Sorting challenges
Not all colorants will be equally easy to recycle, and sorting the colorants will be a key challenge for the project. Some colorants are more complex than others or more costly to process. “Colorants impact recycling in ways that aren’t always visible,” says Jules Roelofs, Global Innovation Manager at Holland Colours. He explains that different colorants require different approaches, which can complicate the recycling process, especially when it comes to detecting and separating colored plastics. “Sorting is crucial,” Roelofs emphasises. “We need to understand the different streams of colorants and determine which ones can be recovered and which might not be worth the effort.”
From research to real-world application
If all goes according to plan, Weckhuysen and Roelofs hope to scale up their project and implement it in practice. “Our ultimate goal is to apply this knowledge and bring the technique to market,” says Weckhuysen. CuRe Technology will play a pivotal role in this effort. This mid-sized company specialises in polyester recycling and has developed an innovative process for continuous polyester recycling. While they currently process several kilograms per hour, their ambition is to expand to installations capable of recycling multiple kilotons annually.
“It would be amazing if we could produce products using recovered colorants,” Roelofs says enthusiastically. “Our ultimate goal is 100% reusability. By extracting colorants from plastics, we can not only reuse the colorants but also preserve the quality of the plastic, enabling it to be recycled more frequently.”
About Circular Plastics NL
Circular Plastics NL aims to drive innovation in the plastics industry to promote a circular economy and is partly funded by the Dutch National Growth Fund. Its focus spans several areas of the plastic recycling process, including improving the quality of recycled materials, removing and reusing additives like colorants, and developing circular methods for various types of plastics. Circular Plastics NL also emphasises innovations in product design to ensure future products are easier to recycle. By fostering collaboration between academia and industry, the initiative envisions a more sustainable future for the plastics industry.
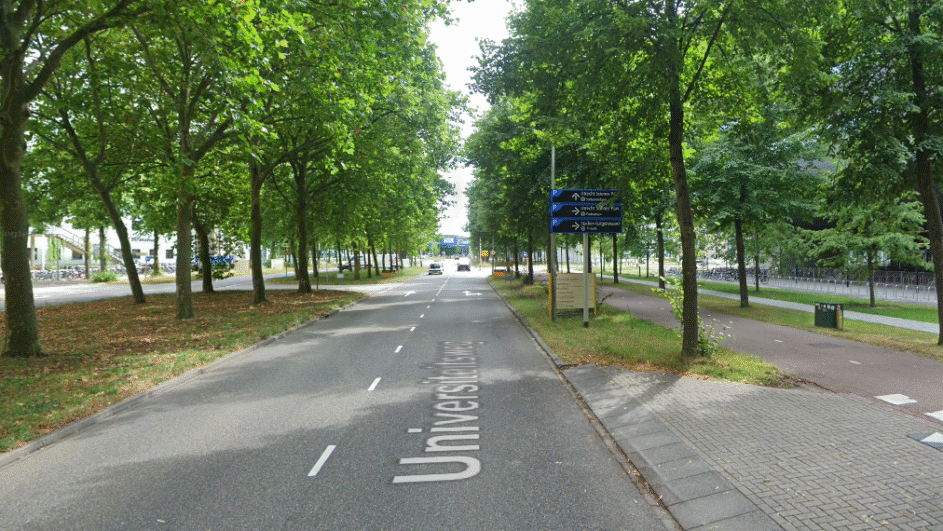
Road maintenance Universiteitsweg
The municipality of Utrecht will renew the Universiteitsweg between July and August with new asphalt and added greenery.
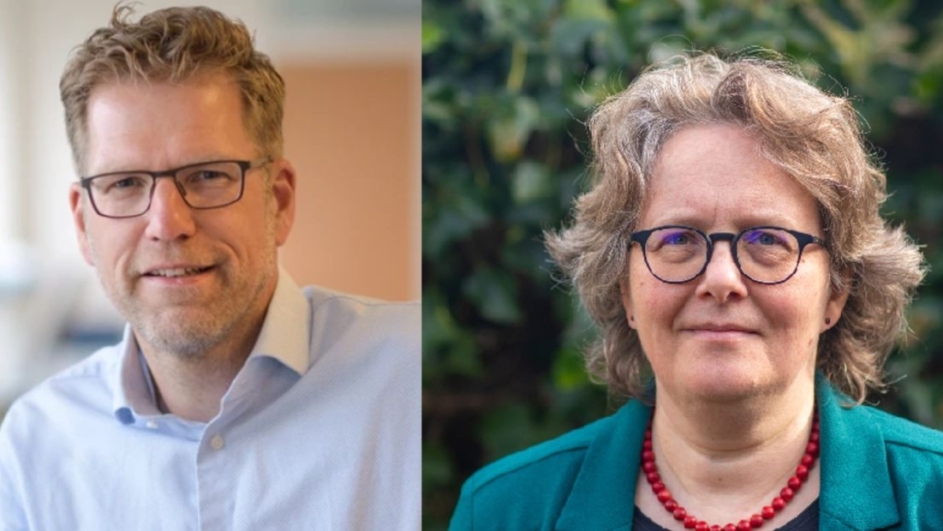
Two researchers from Utrecht receive top Dutch science awards
Researchers Ingrid Robeyns and Thijn Brummelkamp have been awarded the Stevin and Spinoza Prize respectively for their pioneering work on social inequality and genetic research.
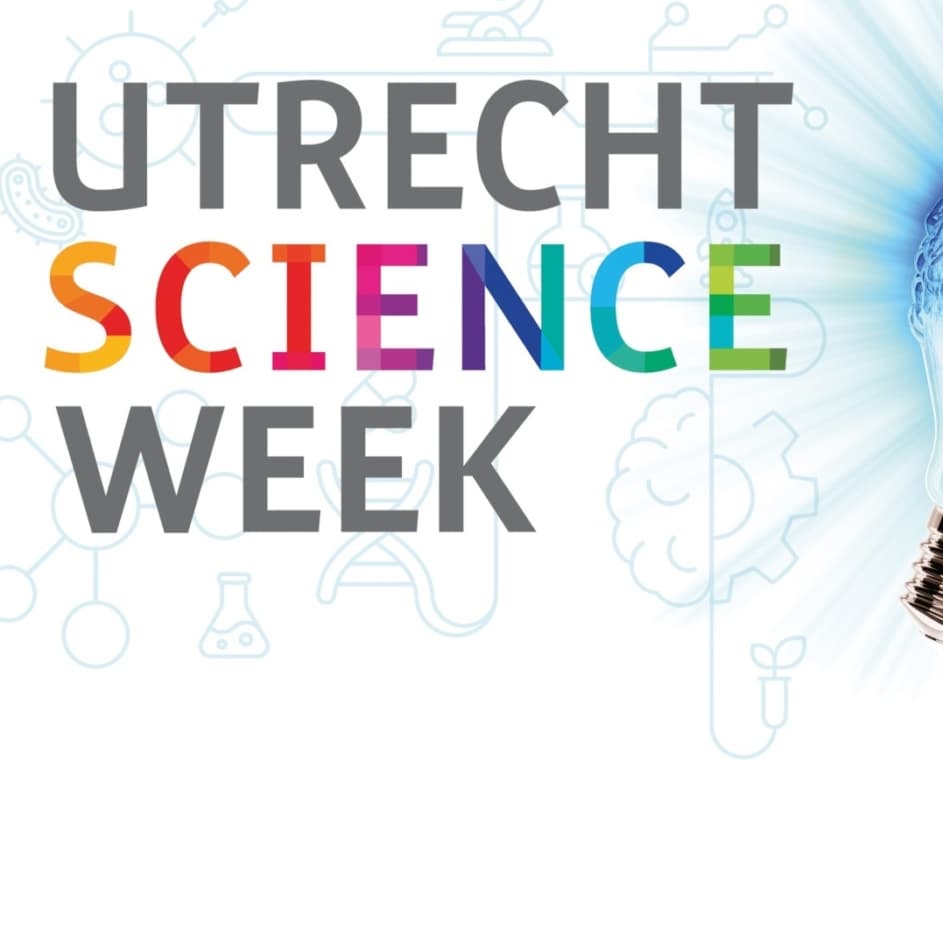
Utrecht Science Week 2025 programme announced
The programme for Utrecht Science Week 2025 has been announced. From now on, you can register for one or more of the many inspiring events. More events will follow in the coming weeks. Take a look, register for the events you would like to attend and don’t miss anything!